EARLY PROBLEM DETECTION AND RESOLUTION
Our inspection and testing procedures at origin are the best way to ensure that the equipment purchased scrupulously complies with the contracted specification, avoiding unpleasant surprises upon receipt at destination.
Many times deviations are detected at the point of installation, but normally the construction milestones of the projects make it impossible to correct or replace the components, so the defects are accepted and a financial compensation is negotiated. The end result inevitably impacts project performance. A quality control at source allows an early detection of problems that will make it possible to correct deviations with a minimum impact on the final result. Our team of quality engineers, equipped with the most modern online reporting tools, will be your eyes and ears in the Asian factories.
90% of field failures can be avoided in the factory.
IN-HOUSE LOCAL TEAMS ALONG THE ENTIRE SUPPLY CHAIN
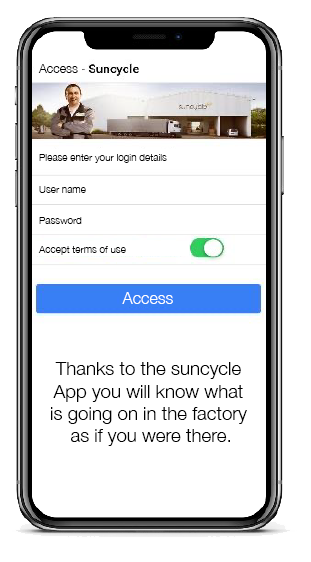
Most critical PV equipment is manufactured in Asia. This fact results in geographical, language and cultural barriers that are often insurmountable.
If we add to this reality the travel restrictions caused by COVID19 , it is necessary for the inspection teams to be local and loyal to the customer.
For this reason, we only carry out inspections with our own staff, duly qualified and knowledgeable in both Asian and Western customs.
We cannot afford to be “lost in translation”!
PLANNING THE QUALITY ENVIRONMENT IN ADVANCE SAVES A LOT OF FUTURE PROBLEMS
MONITORING THE MANUFACTURING PROCESS IS KEY TO THE RELIABILITY OF YOUR PROJECT.
-
Production monitoring.
Once the customer's project is launched to manufacturing our inspectors check daily that the materials used are as agreed, that they are stored correctly and used before their expiration date. Process conditions and equipment calibrations are also checked. Any deviation is transmitted to the manufacturer and the customer immediately, in order to agree and initiate corrective actions and avoid repetitive failures in the product. The customer is part of the process, as Suncycle brings clarity to traditionally obscure areas. Thanks to our digital reporting platform this process occurs in near real time.
-
Pre-shipment inspection.
During contract signing, sampling and acceptance, criteria must be agreed upon to inspect the quality of the product before it is shipped. Upon daily production, our inspectors randomly select a sample of the product and subject it to a thorough inspection that closely reflects the condition of the order. Factory inspection has two decisive advantages over inspections performed in the field: - The sample size can be much larger, since factory resources are used and there are not the limitations of working on a construction site. - In case of rejection, the ability to react is immediate and product can be replaced with minimal impact on project delivery dates. Components are physically and electrically inspected. Particularly critical is the measurement of the power supplied, which must match the power with which the installation has been modelled.
-
Container loading inspection
We witness the loading of containers. Transport from Asia involves a series of manipulations, inspections and movements over which you have very little control, so it is critical to document the condition of each container before it is closed and sealed. At the reception, if damage is detected, it is easier to allocate responsibilities and execute the guarantees of the insurers if we have a clear photo of the state of the container when it left the factory.